Although it’s a well known legal requirement within Health & Safety legislation to undertake a Legionella risk assessment of your water systems, perhaps less well known is the value of undertaking the risk assessment before these water systems are even ‘live’.
In the chronology of water systems management, risk assessment comes at the very beginning. It will identify the risks, recommend ways to minimise those risks and also be critical in the development of the scheme of control going forward. Therefore, a risk assessment should always be undertaken for new builds and refurbishments, and always by a competent risk assessor independent to the installer.
Legionella - Getting things right first time
The latest British Standard BS8680:2020 Water Quality – Water Safety Plans - Code of Practice has specifically stated that “risk assessment should be an ongoing process from the design and specification stage, through to completion”. And the Department of Health’s HTM04-01 Safe Water in Healthcare Premises 2016, explains how risk assessment should be completed for all new projects via consultation with the Water Safety Group (WSG). The intention of both guidance documents appears to be the same, getting things right first time as far as practicable and ensuring there are fewer risks to bear going forward.
When should you complete your Legionella Risk Assessment?
The risk assessment [RA] should be an ongoing process from inception to completion. But risk assessment at all of the following stages should be considered;
- Design & Specification - Undertaking an RA based on inherent risk, gives the WSG the opportunity to see the designer’s intentions and the chance to eliminate unnecessary risks at the initial stage. It’s also a chance to ensure the specification meets the WSG’s requirements, informed via guidance such as HTM 04:01. If there is adequate consultation between designers and the water safety group at this stage, many problems can easily be avoided.
- “First Fix” – This will offer information on how the installation is faring in comparison to the specification, including, pipe-run locations, isolation, access to plant and fittings, built-in dead legs and clinical outlet design.
- “Second Fix” – This will give more information on system performance, including; water temperatures and flow rates, but will also be the last chance to “make good”, before works become costly and impractical.
- Completion – This RA will involve all the above and will show specifically what risks the Water Safety Group will inherently carry forward. Any works required after this point will cause disruption to its intended users.
- Occupation – Once a building is occupied a Legionella Risk Assessments will assess how the designed systems matches the actual water usage and where infrequently used outlets may be present.
Tales from the tap end
The Water Hygiene Centre has worked with many clients at each of these stages and throughout multiple new projects. The following are examples of lessons learnt and valuable information that can be identified during these risk assessments;
- Communication between Projects and Estates teams are improving, but still have a long way to go and involving Estates personnel at the design stage has many benefits.
- Contractors being appointed that do not meet the Water Safety Plan’s training and competence requirements.
- Bacteriological sampling being carried out on the same day as the system chlorination, and not at least 2 days post-chlorination as required.
- Installation of unnecessary thermostatic mixing valves [TMV's] and conversely potential scald risks.
- Re-routing pipework to ensure heavily used outlets are at the end of the water distribution systems lines, thereby assisting water turnover, both within individual rooms and to systems as a whole.
- Unnecessary over-capacity of cold and hot water storage – have you compared design turnover to actual turnover?
- Assets that require on-going maintenance placed in inaccessible areas.
- Servicing valves not sited at tee-joints to eliminate dead legs.
- BMS sensor points not installed at their correct location to aid ongoing monitoring.
- Heat gain issues – cold water tanks sited in warm plantrooms and cold water pipework installed too close to hot water pipework, heating pipework or ceiling radiators.
- Hot water tertiary loops not working effectively, even after balancing.
- Flexible hoses continuing to be fitted, and a lack of pipework insulation behind IPS panels (See Photo Below, which had a Point of use water filter [POUF] fitted!)
- Outlet flushing not being carried out frequently enough, prior to full occupation of the building being reached.
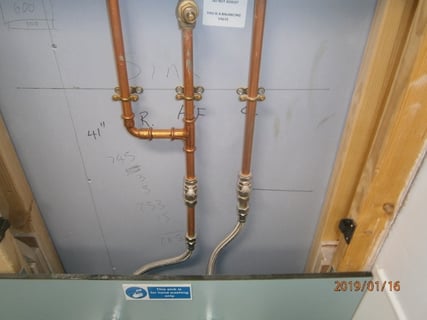
It is also important to know that a Legionella risk assessment at the commissioning stage is neither a tool to “sign-off” a building nor an audit or compliance report for comparison against a specification or standard.
Yes, it will of course highlight aspects of a water system that need rectifying, or holes in documentation that require filling, but primarily a Legionella risk assessment is there to show the water safety group the risks that they want to either eliminate, minimise or accept.
“Derogation” should not be a commonly adopted word or approach in the water safety industry, as it frequently leads to increased risks that subsequently need management.
Conclusion
It is encouraging to see increasing emphasis placed on risk assessment at the early stages of building projects, both from a documented guidance stance and experienced in practice. Estates teams are slowly having more of a say in the extent of “risk” being built into the properties they will need to manage in the future.
The philosophy of “getting it right first time” appears to be reducing headaches, showing financial benefits and most importantly reducing the “risks” to which building users are exposed.
Further reading> Legionella Risk Assessment - Agreeing the terms of reference
Feel free to reach out if you have any questions about this blog or if you would like to consult with one of our experts for further advice on water hygiene.